Executive Summary:
As automation becomes essential for the future of construction, robotic solutions are emerging to solve some of the most repetitive, labor-intensive, and dangerous tasks and provide a safer and more controlled environment to workers.
Nevertheless, there are still many challenges robots must overcome for a successful, and large scale deployment on jobsites, such as the dynamic environment of the worksite, the still high acquisition cost of robots, the need of new training of workers, the adjustment of the traditional workflows, and the overall willingness of construction companies to be open to test these new technologies in their projects. Likewise, off-site production still needs to solve some major barriers such as logistics and size limitations before being able to further scale.
In this article, we’ll walk you through the trends and tailwinds that are currently accelerating the adoption of robots in construction, analyze the current state of construction robotics and finally, share our thoughts on what we expect will come next in the near future.
Why Robots in Construction Now:
For an industry that is the second largest component of world’s GDP and generates more than $12 trillion in revenue annually, construction is still less automated than other sectors and has remained a laggard in terms of innovation.
The fragmented nature of the construction landscape, the disparity of regulations, bespoke designs, and lack of sophisticated management tools are some of the complexities impeding further innovation of the industry. But, several megatrends are now forcing the industry to find new ways of construction to enhance productivity and efficiency of workflows, to improve environmental performance and to provide safer worksites for workers. This has led to the advent of robotics to construction sites. For the purposes of this article, we define a construction robot as any automated / semi-automated machine that assists either on-site or off-site in the construction of buildings.
The most influential trends accelerating the adoption of robotics today are:
- Global labor and skills shortages: the problem of labor shortages is growing in importance and urgency, with the industry struggling with a high number of resignations (perpetuated since the Covid-19 and the “Great Resignation”), a problem of aging workers approaching retirement and a lack of appeal to young generations. Some of the factors preventing more people from entering the industry are the risk of fatalities or injuries happening in construction sites, and the lack of innovation. Automation can not only maximize the existing workforce, but also reduce the worker’s exposure to risks
- Increased scale and complexity of projects: as technology advances, the construction firms are becoming more international and larger and have greater ability to deploy technology across their project sites. This combined with a new age workforce and increased complexity of projects is resulting in increased technology deployments on jobsites
- Sustainability: any future of construction necessarily needs to focus on reducing its environmental footprint, given that it is the industry generating most global greenhouse emissions. Sustainable construction requires finding strategies to build with renewable and recyclable resources and optimizing the building design to reduce waste and energy consumption not only during its construction, but throughout the lifetime performance of the building. Robots enable demolition and recycling of materials, which were previously uneconomical or hazardous, opening up new opportunities for deployment
- Advanced capabilities and reduction of costs: the lowering of the cost of acquisition and greater availability of robotic platforms and parts, together with the advances in computer vision, Internet of Things, and Machine Learning that are improving the capabilities of robots, have facilitated the growth of startups focusing on robotics. Robots are now applicable to broader use cases as they are cheaper, easier to acquire, smarter and more sophisticated, and thus, able to adapt to different surroundings and perform not only repetitive and simple tasks, but more complex and flexible ones. The timeline for robotics development has vastly decreased, making them much more economically viable propositions and easier to scale
- New payment models: a change in the business model is enabling the wider accessibility of robotics to companies. We are moving from the traditional model where machinery / robots were built and owned by the company with high initial investment (one-time capital expenditure – Capex model) to a recurring operating expenditure (recurring fee based on usage – Opex model). This flexibility has unlocked opportunities to deploy robots faster and at much smaller projects
These tailwinds are tipping the scales in favor of the adoption of robotics in construction. This push is mainly coming from big corporations like ABB, Hilti, DPR, Black & Veatch, Autodesk, Trimble, Fischer, Kajima, HP, Bechtel, Schneider (and a host of others), and increasingly, by VC-backed startups willing to disrupt the ecosystem. The adoption however varies significantly by geographies, and countries with extreme labor shortages like Japan are at the forefront of robotic deployments on jobsites. We believe there is a massive potential for robots to improve the status quo.
This market map outlines the current construction robotics startups landscape worldwide:
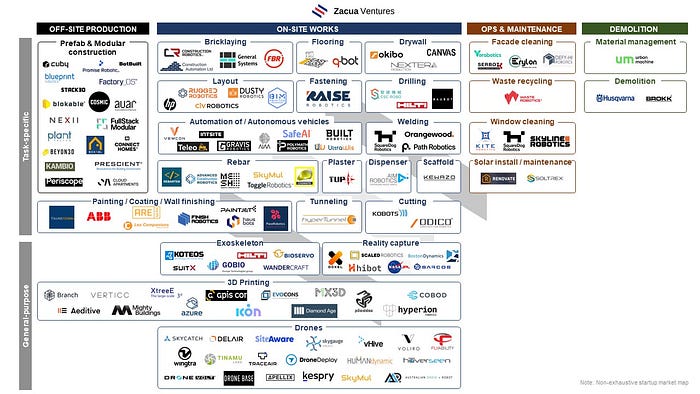
Construction Robotics’ Status Quo:
Now, we will deeper dive into some of these use cases and technologies and their specific challenges for a successful deployment:
1. Aerial Drones
The use of drones in the construction industry has been rising for several years and that’s mainly because of its vast application and low cost. Their aerial vantage and data collecting abilities (through GPS, cameras, thermal or infrared sensors or AI software) make drones a versatile technology whose use can range from security to real-time monitoring. Some of the most popular uses are:
- Mapping and land survey: Drone can monitor any worksite and gather data much faster to build a detailed aerial map that can be turned into a 3D model or digital twin. This allows contractors to identify, analyze and rectify potential issues during the planning phase, thus, ensuring better accuracy of the budget and cutting down time and costs spent on site development, inspection and in the long run execution.
Example of startups: Wingtra, Skycatch, Delair - Monitor and review construction progress: Drones can collect real-time data about the construction process, helping contractors understand what’s happening on their site, track its progression and even identify mistakes that might have occurred. These inspections can be conducted much more seamlessly and efficiently by drones.
Example of startups: Drone Deploy, Traceair, Drone Base, Siteaware - Security and safety surveillance: Drones can use their aerial vantage point to locate equipment and workers, monitor site security and check stability of structures. This technology can not only reduce the risk of equipment being stolen or lost, but more importantly, the risk of fatalities occurring to workers.
Example of startups: Hoverseen
In the near term, drones will likely be able to perform many other activities such as lift materials from one place to another location or be able to direct and guide autonomous vehicles. Nevertheless, the regulations against their usage in many locations and privacy issues are some of the burdens that will need to be overcome. Also, the need for professional training for operators to remotely control the drone and the environmental constraints (especially, wind, dirt, or dust) are hindering its massive adoption. We believe that as the technology advances, the use of drones will continue to grow and will become a mainstream technology in every construction site.
Example of startups: Apellix, VHive, Voliro, Flyability, Kespry, Drone Volt, Tinamu Labs
2. On-site Robots
Imagine walking onto a worksite to find several robots doing some of the repetitive and tedious tasks that were previously done by workers. Imagine a robot laying a brick wall or painting walls, another doing layout or painting or finishing a wall, or even a dozer or excavator moving autonomously. This may seem very futuristic, but improvements in robotic technology are already making this more of a reality.
Robots are today being used to accomplish jobs deemed dangerous, tedious, and repetitive for humans. Some of these examples are:
- Bricklaying robots are being used to perform a task consecutively and efficiently of picking the bricks, putting the mortar on them, and layering the bricks for buildings, roads, or walls. Some of these solutions are fully autonomous once placed and loaded with bricks, whereas some others focus on one of the specific tasks and work along with the mason.
Example of startups: General Systems, Construction Robotics, Fastbrick Robotics - Painting / Finishing robots apply coatings or paintings with great precision and evenness. These robots are ideal as the potentially harmful chemicals involved and the repetitive movements needed can be harmful to workers.
Example of startups: Canvas, ARE23, OKIBO, Finish Robotics, Paintjet, Hausbots, Transforma Robotics - Rebar robots are used to enable the rebar cage installation process, ranging from just tying of the rebars to development of entire rebar cages and their placement.
Example of startups: Advanced Construction Robotics, Skymul (for on-site) and Rebartek, Cognisite and Toggle (for off-site) - Layout robots automate the process of measurement and marking on jobsites. With measurements taking a significant amount of time for every trade during the construction process, the ability to automate this process is a significant efficiency driver in projects.
Example of startups / corporates: Dusty Robotics, Rugged Robotics, HP Siteprint, Civ Robotics, BIM Printer - Façade cleaning / maintenance robots (specially, relevant for skyscrapers) that can work on different kinds of surfaces (primarily glass, but also aluminum, composite panels or marble) and are fully autonomous or remotely controlled by an operator.
Example of startups: Skyline Robotics, SquaredDog Robotics, Erylon, Serbot, Defy Hi Robotics, KITE Robotics, Verobotics - Welding robots are used on steel structures, to weld steel beams together. These can make high precision welds and provide increased maneuverability.
Example of startups: Path Robotics, Orangewood Labs - Exoskeleton suits are wearable machines that work with humans to enhance a task or ability the human body lacks and are meant to increase the strength of the average user, endurance, speed, or agility. These could also allow for injured or disabled workers to work in construction.
Example of startups / corporates: Wandercraft, GOBIO, Koteos, EVO, Levitate Technologies, SuitX, Hilti - Autonomous or self-driving construction equipment are vehicles that do not require any operator or driver to operate them but are controlled through AI and high-level computer programming. These vehicles are available in the form of excavators, cranes, Autonomous Track Loader (ATLs) and dozers, and are programmed for respective tasks, among others, lifting objects, excavating grounds, carrying and placing heavy loads.
Example of startups: Built Robotics, Safe AI, Intsite, Ultrawis, Polymath Robotics, Teleo, Vemcon, AIM vision
The benefits of these technologies are significant. Robots can perform some of the most common tasks in construction more efficiently and quickly than humans, thus, cutting down both personnel hours and the duration of the project, eventually resulting in saving overall costs. In addition to that, the use of these robots decreases human error and fatigue-related issues, which not only improves the overall quality of the tasks by eliminating human mistakes, but more importantly, creates a safer work environment for workers. Therefore, robots can boost on-site productivity and efficiency, as well as safety measures.
Despite the immense value that these technologies bring to the construction industry, these are still some challenges constraining its further implementation:
- The changing environment of the worksite requires robots that are able to adapt to the dynamic, unstructured, and complex construction site and to the different weather conditions which increases cost / complexity of development. With the rapid improvement of the perception stack, this is now becoming easier to solve
- The opposition of unions to its implementation as they might fear a loss of employment of workers, and the demand for professional training to be able to operate some of these technologies and to adapt to new supervisory positions that will appear. The approach here needs to be one of education and identification of the right applications for deployment of robotics
- The high initial investment cost and subsequent maintenance costs which are now much lower than they used to be and are being mitigated by new business models, and
- The need to adapt the current workflows to the presence of robots on the jobsite, as the use of robots will require better scheduling, assignment of tasks, and coordination on the project. To overcome this, human centric design eventually needs to evolve to incorporate elements of efficiency — for example, a basic level of standardization across trades (in drilling holes for example) , incorporation of additional robotic capabilities during design (e.g., carrying capacity, variable designs) and efforts are already underway in this space
We believe the advantages of robotics clearly outweigh the barriers and we will gradually see their integration in the worksite as the advancements in these technologies continue.
3. Industrial Robots
Another trend that is accelerating in the industry is the shift of all or part of the construction process to off-site factories, primarily driven by sustainability, cost and speed considerations. Off-site projects can reduce waste, use less energy, and allow teams to work faster and in a more streamlined way. Despite the immense potential of this type of construction, the technology is not yet at the stage of mass market adoption due to the necessity of scale to make these projects viable. There are several different approaches to off-site construction:
- 3D printing:
Construction 3D printing is the technology used to build entire houses, building components (such as columns), or elements for infrastructures (such as bridges). This technology has evolved over the past decade and has gained a lot of attention for its potential of building cheaper, quicker, and in a more sustainable manner.
These robots can be placed both on-site or off-site in a factory and can take the form of a gantry system (heavier and better suited for mass construction) or a robotic arm (more freedom of movement and adaptable), providing great flexibility on the design and potential customization of the construction. Compared with traditional methods, 3D printing can significantly reduce the time of construction and requires less workers involved, thus, helping overall be more productive in the construction process. Also, it is more cost-efficient as it allows for more precise amounts of materials and for the use of alternative materials (including waste-by-products, plastics, or glass), thus, reducing the generation of waste and the environmental footprint.
Nonetheless, one of the trickiest parts of 3D printing is finding the right mixture of materials as placing a series of layers on top of the other requires the material to have the right density to be placed correctly but needs to harden quickly to hold and maintain the shape and qualities over time. Another issue is the decision around placing the printer in a factory, which adds the complexity of logistics and the potential damage of the structures during its shipping, or to place it in the jobsite where the job is exposed to changing environmental conditions, which makes it harder to place and to control the quality of production. In practice, most of the startups tend to print on-site and look for solutions (e.g., tents or shield structures) to control and protect the printing. Reinforcement is also a challenge in 3D printing as fitting the rebar is complex and thus, solutions either leave the concrete unreinforced, or do this process manually.
Example of startups: COBOD, ICON, Evocons, Hyperion Robotics, Apis cor, Diamond Age, 3DPlodder (for on-site), and Aeditive, Mighty Buildings, Branch technology, Vertico, Azure Printed Homes, Xtreee (for off-site)
- Prefabrication:
Prefabricated construction refers to the building or sections of a building that are manufactured in a factory prior to its final assembly at the construction site. It permits standardization and mass customization with prefabricated elements to adapt to the different designs.
Modular construction is a type of prefabrication and consists of the building of repeated modules (that box-like structures or units) being mostly built in the factory and then transported on site. Similar to the 3D printing off-site, given that the work is mostly done in the factory with a standard and fixed line of production, the challenges inherent to the jobsite are removed and have the advantage of being more cost and time-efficient, improve the consistency and quality of the construction and have a safer and less invasive method of the environment. However, logistics remains its major barrier, together with the size limitations of this type of construction.
Example of startups: Automated Architecture, Plant Prefab, Factory_OS, Nexii, Connect Homes, Blokable, Blueprint Robotics, Full Stack Modular, Prescient, Kambio, Cosmic Buildings, Bloxabl, Promise Robotics
What we Expect Moving Forward:
Recent years have seen a decline in the cost of platforms, and an improvement in the capabilities of robotics, which has led to a use of robots in a wider range of applications. The lack of labor, the need for higher productivity and the pressures from the market and the institutions are encouraging the construction companies to be more open to the deployment of robots in order to find new methods of construction that are more efficient, more sustainable, and safer. But the industry still needs many more robots.
In the short term, we expect more technologies will come to solve specific pain points of the whole value chain. Robots will take over the tiresome and hazardous tasks (e.g., material handling, fastening, electrical works), and also be applied to new use cases (e.g., the re-use or circularity of materials), enabling workers to focus on more value-added tasks.
However, to fully unlock the capabilities of robots, we believe construction projects will need to be adapted from the design stage to account for the presence of robots during the entire process of construction. This coupled with evolution of robots from task-specific to multi-purpose robots will broaden usage of robots in applications that aren’t apparent today.
Robots are now slowly entering the industry to work alongside workers to augment their work, keep them safer and boost productivity, and as more companies start to test and deploy these solutions, the industry will see a boost in the development of new solutions with a wider set of capabilities, providing a unique space for robotics applications to grow and scale.
As an active investor, Zacua Ventures will continue to look for the emerging solutions in the robotics space, searching for the right technologies and startups to be supported in their journey.